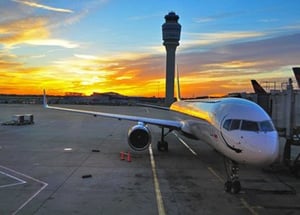
Contributed by Mike Flora
The main purpose of a coating is to protect against corrosion. However, corrosion can quickly arise if defects such as pinholes develop while the coating is applied. The best coatings reduce or eliminate the occurrence of pinholes for the most challenging use cases.
What are Pinholes?
Pinholes are a defect in the coating that
Why Pinholes are Undesirable?
The presence of pinholes indicates a quality issue. Pinholes provide a path of exposure to the metal substrate and can leave the metal vulnerable to corrosion, thus preventing the coating from achieving its purpose of protection. Pinholes also provide a path for the unwanted conduction of electricity from one part to another part in an assembly.
Pinholes negatively impact the adhesion between the metal and the coating. Failure to bond to a substrate defeats the purpose of any coating. As a
The 4 Key Properties of a Good Anti-Corrosion Coating
Good coatings share a number of important characteristics. The most important include:
It Fills Pinholes and Creates an Impervious Barrier
First, and most importantly, a good coating is designed to eliminate existing pinholes and create an impervious barrier, free from pinholes, cracks and other holidays. This property is equivalent to self-leveling concrete, in that it automatically fills in little imperfections or holes that formed due to areas where the coating didn’t adhere, or where the coating application was too thick or too thin.
It Can Adhere to a Number of Different Substrates
Another desirable characteristic is the coating’s ability to adhere to many different types of metals and composites. This makes the coating more versatile and allows a single coating product to be used for structures that consist of several subassemblies made of different materials.
It Can Tolerate a High Range of Temperatures and Conditions
The ability to tolerate high and low temperatures, and to resist fuels and other substances that can damage the coating, is also important for some purposes.
It Stops Electrical Conduction
Good coatings are also anti-conductive. Cathodic protection (CP) – a method for controlling the corrosion of metallic structures in contact with electrolytically conducting environments such as soil and seawater – is often used in conjunction with coatings for protection. In these systems, an electric current passing through the metal can free hydrogen atoms, causing coating disbondment when the current forces the coating away from the metal. The current can only pass through some sort of fault in the metal’s coating. If the coating is not susceptible to pinholes, then cathodic disbondment does not occur. Being anti-conductive is an important characteristic for some specialized applications. We’ll discuss this in more detail below.
Ultimately, the end goal is to prevent corrosion, so any anti-corrosive properties that the coating contains are helpful.
Demanding Applications Require a Premium Coating Product
There are many types of coatings available, but a key coating product that fulfills many of the properties essential to corrosion prevention mention here is a liquid-nylon coating. The following applications can benefit from a liquid-nylon coating product.
Aviation and Aerospace
Aircraft present two extraordinary challenges to coating engineers. First, there are stringent government regulations that aircraft manufacturers must observe. Second, aircraft contain sophisticated avionics devices including radios, radars, global position systems (GPS) and in some aircraft fly-by-wire controls. If an aircraft is hit by lightning then the electrical current surge can propagate to and damage the avionics. A liquid-nylon coating can stop this electrical charge.
Aircraft contain electrical bonding points such as flap track beams, dry mast assemblies, wire harness assemblies, galleys, cabin seat connections to the airframe, lavatories, hydraulic systems and the center wing box that must be electrically isolated from stray currents. Aircraft designers go to great lengths to design it so. A good example is a flap track beam wire harness assembly, which has a sheathing surrounding it. The sheathing must be coated with a product that does not leave any pinholes.
Marine
Preventing corrosion in anything constantly exposed to water and salt is always problematic. Pinholes provide a path for moisture to penetrate to the underlying substrate. Good coatings are able to pass the ASTM B117 salt-spray or salt-fog test, which is a very common corrosion test to measure corrosion resistance on coated metals.
Automotive
Liquid-nylon coatings are ideal for automobile undercarriages, which are periodically subjected to water and highly corrosive road de-icing treatments.
Construction Products
Liquid-nylon coatings are sometimes appropriate for materials used in the construction industry such as the building stainless steel that is used for stairway railings.
Application Methods
There are three ways to apply a coating. Application with a paintbrush is most common because not only is it the easiest to do but also because the number of applications that can occur on the finished product. The least common method is by dipping the part into the coating. This is the least preferable because of a buildup of excess coating at the bottom or lowest point of the part due to gravity after the part is removed from the coating bath. Sometimes application with a paint sprayer is indicated because it gives a more uniform looking appearance, but this is less common because the main purpose is to protect a part; how the part looks after it is coated does not generally impact the application.
When first applied, a liquid-nylon coating is about the thickness of a piece of paper. It is permissible to apply multiple coats once the preceding coat is tack-free.
After a cure time of 72 hours the coating will be thin and transparent, and look like a piece of cellophane.
Case Study: Liquid Nylon Coatings for Aircraft
As previously mentioned, aircraft contain sophisticated avionics devices that can be damaged if an electrical current from a lightning strike is able to propagate throughout the aircraft. Although small in size, pinholes provide a propagation path.
An aircraft manufacturer can apply a liquid-nylon coating with a brush on approximately two hundred locations throughout the aircraft. Each part is relatively small and is coated prior to the “skin” of the aircraft being installed. This type of application precludes the use of spraying.
Additionally, not all parts are coated during the production phase of the aircraft. Some are coated prior to installation and then installed. An example are wire harness assemblies, which are a series of electrical wires covered with a sheathing to protect the wire. The wire harnesses are typically manufactured at a separate location than the aircraft. Groups of wires are bundled together and held together with a strap. In this instance, a liquid-nylon coating is used to coat the sheathing under the strapping mechanism to prevent it from fraying and exposing the wires. Once completed, the wiring is installed in the aircraft. Generally, this wiring can be found in the non-visual areas of the cabin, such as behind the overhead storage.
The liquid-nylon coating is usually applied to small areas or locations. Even on the center wing box, which is extremely large, only the electrical bonding points receive the coating.
A liquid nylon coating works to eliminate pinholes and prevent some of the other key contributors to corrosion. It is a single-spray, simple-to-apply solution that’s appropriate for many industries.